A traditional process of dyeIng:
The procedure of organic dye started in the year of 2019, in the month of June at our work studio, Pearson Pally, Shantiniketan, (West Bengal, India). Dyeing with organic elements which can be picked up easily from nature or from kitchen waste: like onion skin, pomegranate skin, carrots, eucalyptus etc, was real fun.
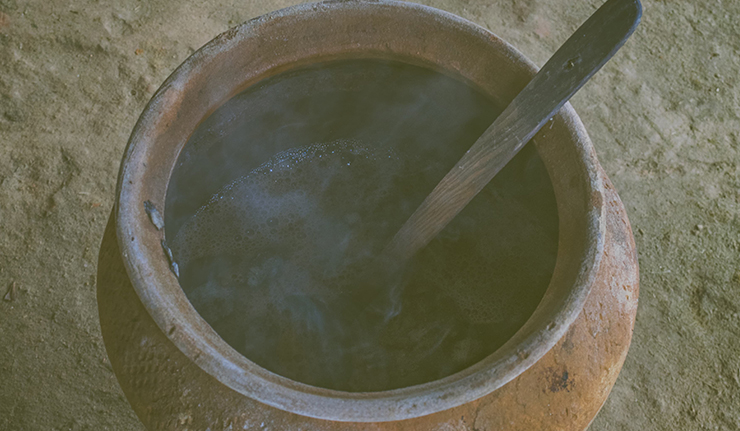
So far, we have officially disclosed the results of dyeing method with, Myrobalan, Catechu, Madder, Bark of piyash tree (we found that tree in the local jungle with the help of a villager, whose grandparents used to follow the process of organic dyeing). The results were amazing and going to the jungle with the local tribals and rediscovering the history of organic dye was sheer happiness.
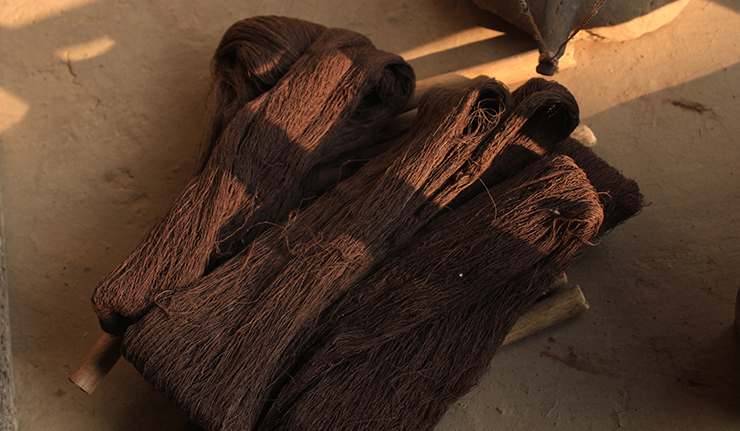
We follow a slow method of dyeing, starting from taking a traditional mud pot to collecting local water to the dyeing components, we try to collect everything from nature and keep it raw or untouched by human mind! Then we follow the boiling process to get the extract from the dye material and after giving it a good filter we collect the colour in a base and we let the yarn or the fabric sit there for a minimum of one hour! And then giving it a good rinse, we let the coloured yarn or the fabric soak in a mordant and thus the outlook of a shade or a definite colour is created!
Following a traditional process of dye is like a good meditation, where you barely think about the output: you only enjoy the art of creation or you are excited to witness the magic!
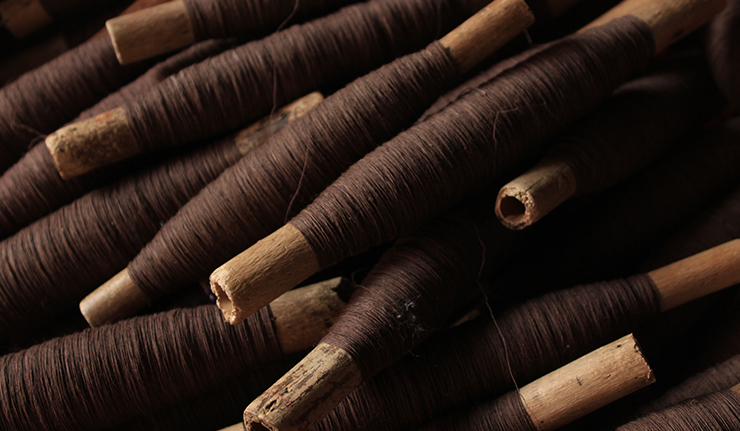
The traditional process of weaving:
Yarn: choosing your yarns can be a difficult story to go for; keeping that in mind we always go for an organic yarns and we scrutinize the every little detail of it: like from where the cotton is sourced and then who are spinning the yarns, is it the women or the men of the village, how long it takes to get a shape and if the wages are open-minded for the artisans etc. seeing all the factors and after doing a quality check every time, we finalize the yarns!
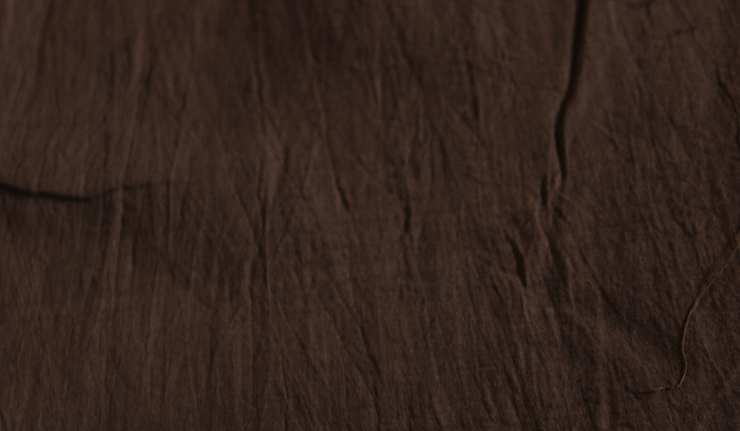
Fabric: the process of choosing the fabric follows the same method like yarns. We mostly work on khadi or hand spun cotton, jamdani, sometimes on organic Ghicha silk, matka silk and Bangalore silk also! We work on a variety of hand spun cotton, from 0 count to 150 count mostly.
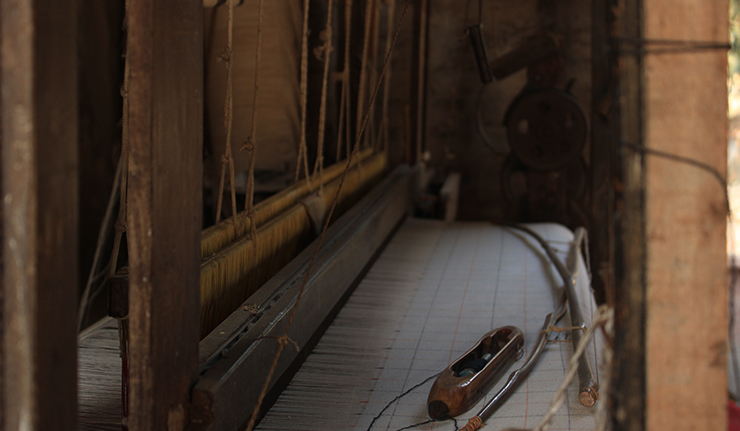
Weaving: once the yarn is dyed then it goes for weaving. We always go for hand weaving, seeing the need for slow textiles, the major waste in the ecosystem comes from the fashion industry or today’s textile world. A huge amount of carbon is released in the ecosystem, as a large number of fashion houses follow the mantra of fast fashion and the waste directly goes to nature. We keep in mind the relevance of our traditional technique while creating a piece of fabric. We purposely pick slow textiles, hand spun, hand woven and handmade when it comes to fashion or textile!
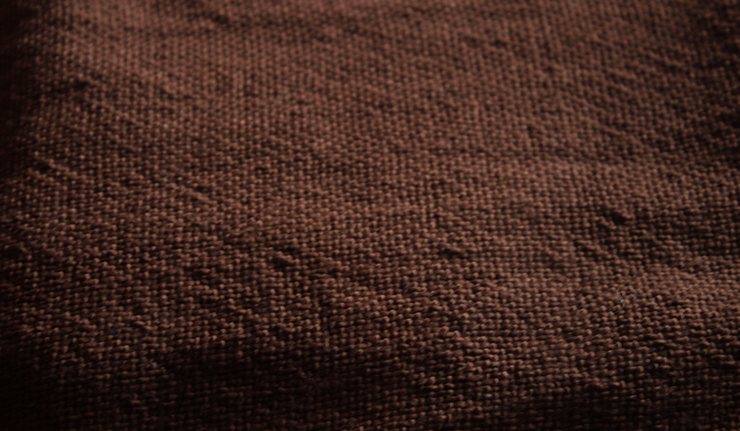
Designing:
We choose our design carefully, seeing the final shade of the fabric we draw the patterns. And afterward the pattern is completed, the fabric is designed. And thus, every piece is created with a lot of care and love, and they all are unique in their own style. And creating every piece takes a lot of effort and time, with each design: we create a story and the design itself tells the story!
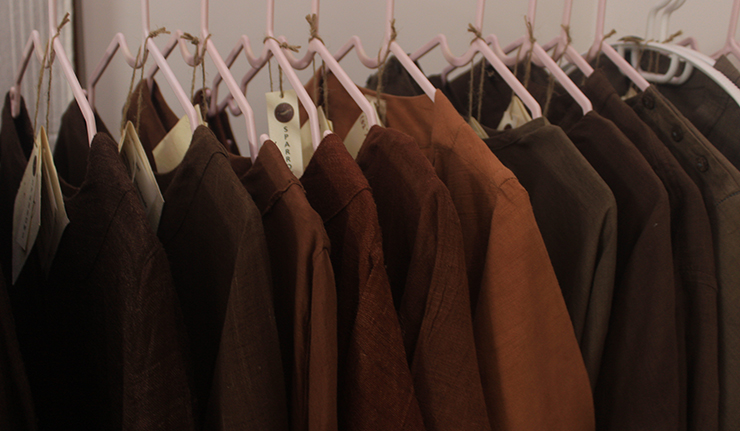
Making:
While reaching the final stage of the process, shipping comes: we consciously select the materials of the packing: creating a nice regular canvas bag and preparing the tag or the label, we try to keep it real and organic. We all have felt some sort of discomfort while wearing a new piece, in our childhood, while growing up, in our adulthood. We all have gone through the same experience: an uneasiness in our necks and the labels and we did not have any choices but to keep the labels or tear it. Keeping that in mind, we chose the material of the label as soft as possible, nice hand spun cotton pieces! The tags also come with a friendly direction on how to wash and dry the piece.
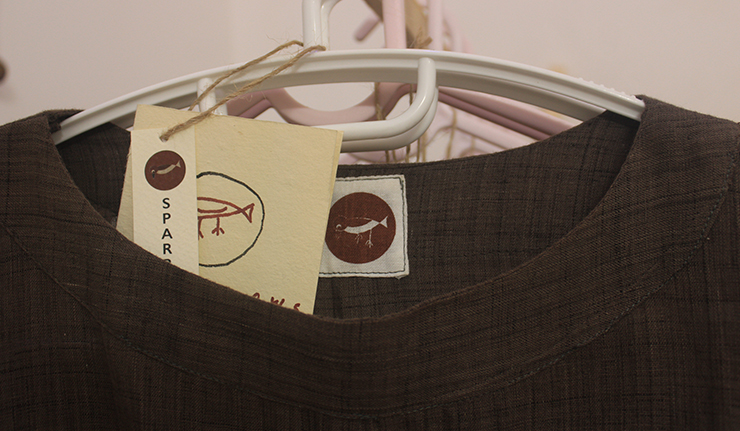